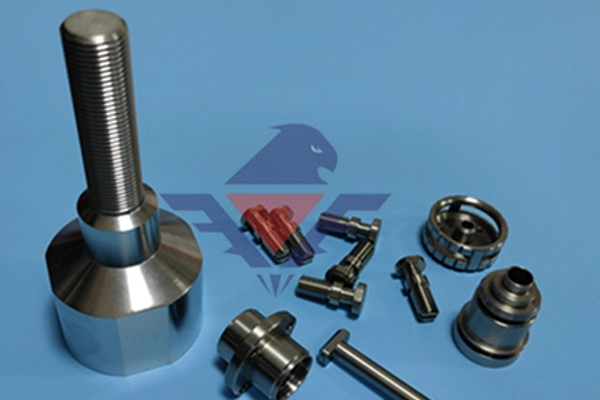
# Swiss Machining: Precision and Efficiency in Small Part Manufacturing
## The Evolution of Swiss Machining
Swiss machining, also known as Swiss screw machining or Swiss turning, has revolutionized the manufacturing of small, precision parts. Originating in Switzerland’s watchmaking industry during the 19th century, this specialized machining technique was developed to meet the exacting standards required for tiny watch components.
## How Swiss Machining Works
Unlike conventional lathes, Swiss machines feature a sliding headstock that moves the workpiece while the cutting tools remain stationary. This unique configuration provides several advantages:
– Enhanced precision for long, slender parts
– Reduced vibration during machining
– Ability to perform multiple operations simultaneously
– Improved surface finishes
## Key Benefits of Swiss Machining
### 1. Exceptional Precision
Swiss machines can achieve tolerances as tight as ±0.0001 inches (0.0025 mm), making them ideal for medical devices, aerospace components, and electronics.
### 2. High Production Efficiency
The simultaneous machining capability allows for faster cycle times compared to traditional methods. Many Swiss machines can complete complex parts in a single setup.
### 3. Material Savings
The precise control over material feeding minimizes waste, particularly important when working with expensive materials like titanium or specialty alloys.
## Applications Across Industries
Swiss machining has found widespread adoption in various sectors:
– Medical: Surgical instruments, implants, and dental components
Keyword: Swiss Machining
– Aerospace: Fuel system parts, fasteners, and sensor components
– Automotive: Fuel injection parts, transmission components
– Electronics: Connectors, contacts, and miniature housings
## Modern Advancements in Swiss Technology
Contemporary Swiss machines incorporate cutting-edge features:
– Multi-axis capabilities (up to 13 axes)
– Live tooling for milling and drilling operations
– Automated bar feeders for continuous production
– Advanced CNC controls with predictive maintenance
## Choosing the Right Swiss Machining Partner
When selecting a Swiss machining provider, consider:
– Experience with your specific industry requirements
– Quality certifications (ISO, AS9100, etc.)
– Material expertise
– Capacity for prototyping and high-volume production
– Secondary services (finishing, assembly, etc.)
Swiss machining continues to push the boundaries of what’s possible in precision manufacturing, enabling the production of increasingly complex miniature components that power modern technology across countless industries.