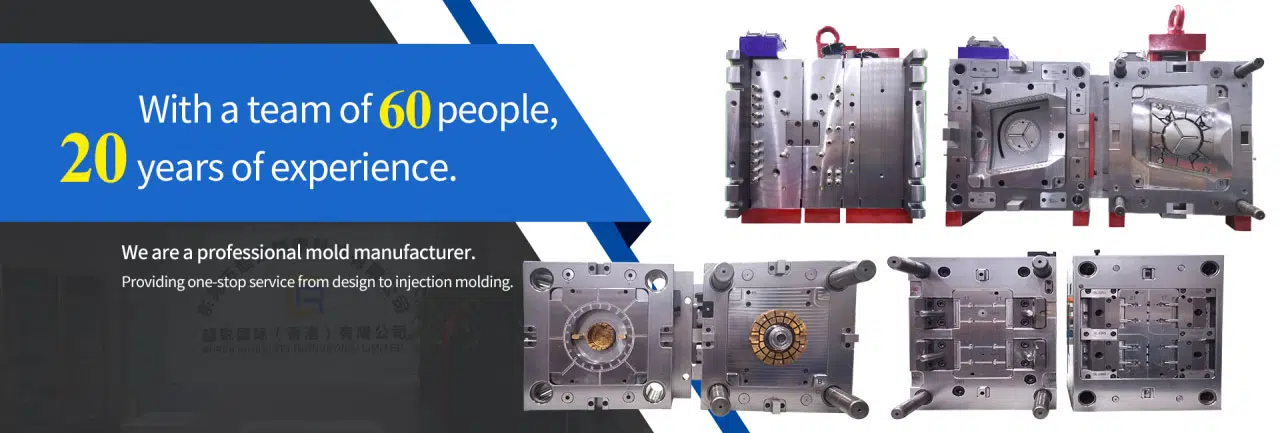
# Rapid Prototyping and Tooling for Efficient Product Development
## The Importance of Rapid Tooling in Modern Manufacturing
In today’s fast-paced manufacturing environment, rapid tooling has become an essential component of efficient product development. This innovative approach allows companies to create prototype and production tools quickly, reducing time-to-market and enabling faster iterations during the design process.
Rapid tooling bridges the gap between prototyping and full-scale production, offering manufacturers the ability to test designs with production-grade materials before committing to expensive, permanent tooling solutions.
## Key Benefits of Rapid Prototyping and Tooling
### 1. Accelerated Development Cycles
By implementing rapid tooling techniques, companies can significantly shorten their product development timelines. Traditional tooling methods often require weeks or months to complete, while rapid tooling solutions can deliver functional prototypes or low-volume production parts in a matter of days.
### 2. Cost-Effective Design Validation
Rapid tooling enables manufacturers to test their designs with actual production materials at a fraction of the cost of conventional tooling. This early validation helps identify potential issues before committing to large-scale production, saving both time and money.
### 3. Flexibility for Design Changes
Unlike traditional tooling methods that are difficult and expensive to modify, rapid tooling allows for easier design adjustments. This flexibility is particularly valuable during the iterative design process when multiple versions may need testing.
## Common Rapid Tooling Technologies
Several technologies have emerged as leaders in the rapid tooling space:
– 3D Printed Tooling: Additive manufacturing techniques create molds and tooling inserts directly from digital designs
– Soft Tooling: Uses less durable materials like silicone or aluminum for short production runs
Keyword: Rapid Tooling
– Bridge Tooling: Intermediate solutions between prototyping and full production tooling
– Direct Metal Tooling: Metal 3D printing for more durable production-grade tools
## Applications Across Industries
Rapid tooling finds applications in numerous industries:
– Automotive: For prototyping new components and low-volume production
– Consumer Electronics: Enabling faster iteration of product designs
– Medical Devices: Supporting the development of customized solutions
– Aerospace: Creating lightweight components with complex geometries
## Best Practices for Implementing Rapid Tooling
To maximize the benefits of rapid tooling, consider these best practices:
– Start with clear design requirements and production goals
– Choose the appropriate rapid tooling method based on material requirements and production volume
– Work closely with experienced rapid tooling providers
– Plan for potential design iterations
– Consider the total cost of ownership, not just initial tooling costs
## The Future of Rapid Tooling
As manufacturing technologies continue to advance, rapid tooling solutions are becoming more sophisticated and accessible. The integration of artificial intelligence for design optimization, improved materials for tool longevity, and faster production methods are all contributing to the evolution of this field.
Companies that embrace rapid tooling as part of their product development strategy will gain a competitive advantage through faster innovation cycles, reduced costs, and the ability to respond more quickly to market demands.