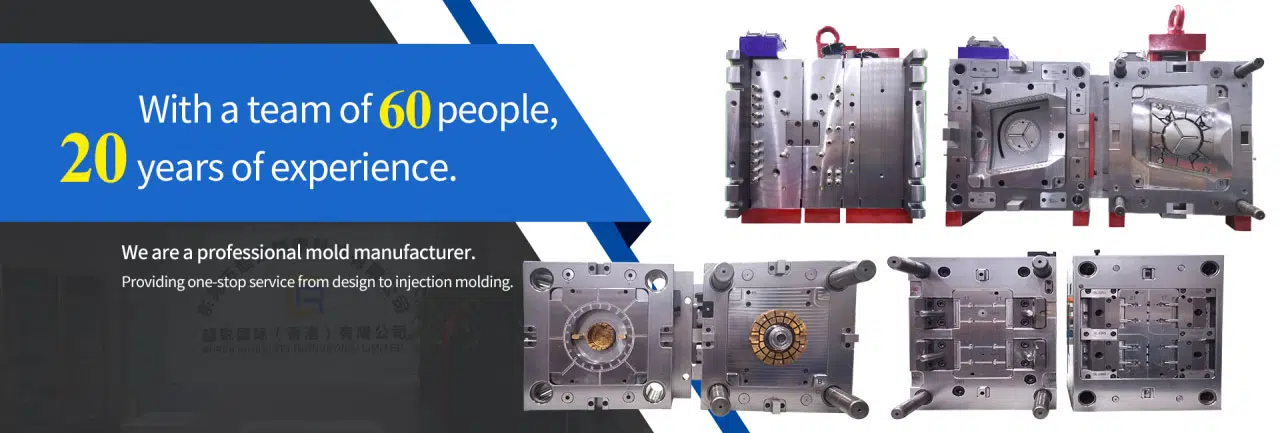
# Sheet Metal Fabrication Techniques and Applications
## Introduction to Sheet Metal Fabrication
Sheet metal fabrication is a versatile manufacturing process that involves transforming flat metal sheets into various shapes and structures. This process plays a crucial role in numerous industries, from automotive to aerospace, construction to electronics. The ability to manipulate metal sheets into precise components makes this technique indispensable in modern manufacturing.
## Common Sheet Metal Fabrication Techniques
### 1. Cutting
Cutting is the fundamental first step in sheet metal fabrication. Several methods exist:
– Shearing: Uses straight blades for straight cuts
– Laser cutting: High-precision method using focused laser beams
– Plasma cutting: Effective for thicker materials
– Water jet cutting: Uses high-pressure water for clean cuts
### 2. Bending
Bending transforms flat sheets into angular shapes:
– Press brake bending: Most common method using a punch and die
– Roll bending: Creates curved surfaces like cylinders
– Folding: Produces sharp bends with specialized equipment
### 3. Punching
Punching creates holes or specific shapes in metal sheets:
– Turret punching: Uses multiple tools for various hole patterns
– CNC punching: Computer-controlled for high precision
– Perforating: Creates patterns of small holes
### 4. Welding
Welding joins metal pieces together:
– MIG welding: Versatile and commonly used
– TIG welding: Produces high-quality welds
– Spot welding: Efficient for joining thin sheets
## Advanced Fabrication Methods
Modern sheet metal fabrication incorporates several advanced techniques:
### Laser Cutting Technology
Laser cutting has revolutionized precision cutting with:
– Minimal material waste
– High repeatability
– Complex shape capabilities
– Clean edges requiring little finishing
### Hydroforming
Keyword: Sheet Metal Fabrication
This innovative technique uses fluid pressure to form metal:
– Excellent for complex shapes
– Reduces tooling costs
– Improves material strength
– Creates seamless parts
## Materials Used in Sheet Metal Fabrication
Various metals are suitable for fabrication:
Material | Properties | Common Applications
Steel | Durable, strong | Automotive, construction
Aluminum | Lightweight, corrosion-resistant | Aerospace, electronics
Copper | Excellent conductivity | Electrical components
Brass | Decorative, corrosion-resistant | Architectural, musical instruments
## Applications Across Industries
Sheet metal fabrication serves numerous sectors:
### Automotive Industry
– Body panels
– Chassis components
– Exhaust systems
– Engine parts
### Aerospace Sector
– Aircraft skins
– Structural components
– Engine housings
– Interior fittings
### Construction Field
– Roofing materials
– HVAC ductwork
– Structural supports
– Decorative elements
### Electronics Manufacturing
– Enclosures and cases
– Heat sinks
– Shielding components
– Mounting brackets
## Quality Control in Sheet Metal Fabrication
Maintaining quality is essential throughout the fabrication process:
– Dimensional accuracy checks
– Surface finish inspections
– Material thickness verification
– Weld integrity testing
– Stress and load testing
## Future Trends in Sheet Metal Fabrication
The industry continues to evolve with:
– Increased automation and robotics
– Advanced simulation software
– Sustainable manufacturing practices
– Integration with IoT technologies
– Development of new alloys and composites
## Conclusion
Sheet metal fabrication remains a cornerstone of modern manufacturing, offering versatility, precision, and efficiency across countless applications. As technology advances, the processes continue to improve, enabling more complex designs and higher quality products. Understanding these techniques and their applications helps businesses make informed decisions about their manufacturing needs.