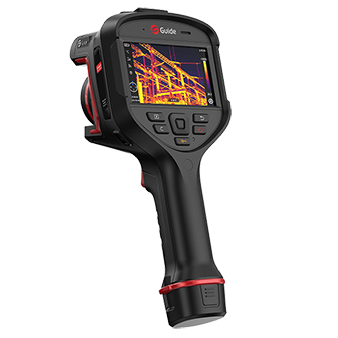
# Thermography Inspection Solutions for Industrial Applications
## Introduction to Thermography Tools
Thermography tools have revolutionized the way industries approach maintenance and quality control. These non-contact, non-destructive testing methods utilize infrared imaging to detect temperature variations that indicate potential issues in equipment, structures, and processes. As industrial operations become more complex, thermography inspection solutions offer a critical advantage in predictive maintenance and operational efficiency.
## Key Applications of Industrial Thermography
### Electrical Systems Monitoring
Thermography plays a vital role in electrical maintenance by identifying hot spots in switchgear, transformers, and distribution panels. These temperature anomalies often precede catastrophic failures, allowing for timely intervention before costly downtime occurs.
### Mechanical Equipment Analysis
Rotating machinery such as motors, pumps, and bearings can be effectively monitored using thermal imaging. Abnormal heat patterns indicate friction issues, misalignment, or lubrication problems that might otherwise go unnoticed until complete failure.
### Building and Infrastructure Inspection
Thermography tools help identify energy leaks in building envelopes, moisture intrusion in walls, and structural defects in bridges and other critical infrastructure. This application is particularly valuable for preventive maintenance programs.
## Advanced Features of Modern Thermography Tools
Today’s thermography solutions offer more than just temperature measurement. Advanced features include:
– High-resolution thermal imaging with precise temperature measurement
– Automated analysis and reporting capabilities
– Integration with predictive maintenance software
– Portable and rugged designs for field use
– Wireless connectivity for real-time data sharing
## Benefits of Implementing Thermography Solutions
Industrial facilities that adopt thermography inspection solutions experience numerous advantages:
Reduced downtime through early fault detection
Improved worker safety by minimizing physical inspections of live equipment
Energy savings through identification of thermal inefficiencies
Extended equipment lifespan with proactive maintenance
Comprehensive documentation for compliance and audit purposes
## Choosing the Right Thermography Solution
When selecting thermography tools for industrial applications, consider these factors:
Temperature Range and Sensitivity
Ensure the device can accurately measure the expected temperature variations in your specific application.
Image Quality and Resolution
Higher resolution provides more detailed thermal images for precise analysis.
Environmental Considerations
Choose equipment rated for the conditions in your facility (dust, moisture, explosive atmospheres).
Software and Analysis Capabilities
Advanced software can significantly enhance the value of your thermal data through automated analysis and trending.
## Future Trends in Industrial Thermography
Keyword: Thermography Tools
The field of thermography continues to evolve with emerging technologies:
– Integration with AI for automated fault detection
– Combination with other NDT methods for comprehensive analysis
– Miniaturization of sensors for embedded monitoring
– Enhanced data analytics for predictive maintenance algorithms
– Cloud-based solutions for enterprise-wide thermal monitoring
As industries increasingly prioritize efficiency and reliability, thermography inspection solutions will remain at the forefront of maintenance technology, helping organizations prevent failures, reduce costs, and optimize operations.