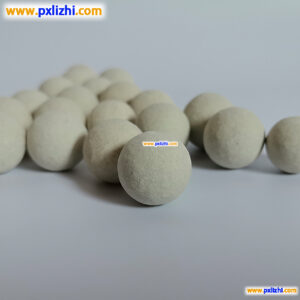
# Ceramic Ball Manufacturing Process and Applications
## Introduction to Ceramic Balls
Ceramic balls are precision-engineered spherical components made from advanced ceramic materials. These balls offer exceptional properties that make them suitable for a wide range of industrial applications where high performance and durability are required.
## Manufacturing Process of Ceramic Balls
### 1. Raw Material Selection
The manufacturing process begins with the careful selection of ceramic materials. Common materials used include:
– Alumina (Al2O3)
– Zirconia (ZrO2)
– Silicon Nitride (Si3N4)
– Silicon Carbide (SiC)
### 2. Powder Preparation
The selected ceramic powder is mixed with binders and additives to create a homogeneous mixture. This step is crucial for ensuring consistent material properties throughout the manufacturing process.
### 3. Forming Process
There are several methods for forming ceramic balls:
– Isostatic Pressing: Powder is compressed in a flexible mold under high pressure
Keyword: ceramic ball
– Extrusion: Material is forced through a die to form spherical shapes
– Injection Molding: Ceramic powder mixed with binder is injected into molds
### 4. Sintering
The formed balls undergo sintering in high-temperature furnaces (typically 1400-1800°C). This process causes the ceramic particles to bond together, creating a dense, strong structure.
### 5. Precision Grinding and Polishing
After sintering, the balls undergo precision grinding and polishing to achieve:
– Tight dimensional tolerances (often within microns)
– Superior surface finish (Ra < 0.01 μm)
– Perfect sphericity
### 6. Quality Control
Each ceramic ball undergoes rigorous quality checks including:
– Dimensional inspection
– Surface quality assessment
– Mechanical property testing
– Roundness measurement
## Applications of Ceramic Balls
### 1. Bearings
Ceramic balls are widely used in high-performance bearings due to their:
– High hardness and wear resistance
– Corrosion resistance
– Light weight (40% lighter than steel)
– Ability to operate without lubrication
### 2. Valves and Pumps
In fluid handling systems, ceramic balls provide:
– Excellent chemical resistance
– Long service life
– Reduced maintenance requirements
– Improved sealing performance
### 3. Medical Applications
Ceramic balls find use in medical devices because of their:
– Biocompatibility
– Sterilizability
– Wear resistance in joint replacements
### 4. Aerospace and Defense
The aerospace industry utilizes ceramic balls for:
– High-temperature applications
– Reduced weight components
– Wear-resistant parts in harsh environments
### 5. Electronics and Semiconductors
In precision industries, ceramic balls serve as:
– Insulating components
– Wear-resistant guides
– Precision positioning elements
## Advantages of Ceramic Balls
Ceramic balls offer numerous benefits over traditional metal balls:
– Higher hardness and wear resistance
– Better corrosion resistance
– Lower density (reduced weight)
– Higher temperature capability
– Non-magnetic properties
– Electrical insulation
– Longer service life
## Conclusion
The manufacturing of ceramic balls requires precise control at every stage to produce components with exceptional properties. As technology advances, ceramic balls continue to find new applications across various industries, offering solutions where traditional materials fall short. Their unique combination of properties makes them indispensable in demanding environments where performance and reliability are critical.