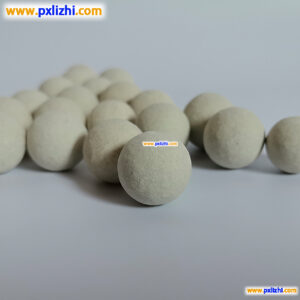
# Ceramic Ball Manufacturing Process and Applications
## Introduction to Ceramic Balls
Ceramic balls are precision-engineered spherical components made from various ceramic materials. These balls offer exceptional properties such as high hardness, wear resistance, chemical inertness, and thermal stability, making them valuable in numerous industrial applications.
## Manufacturing Process of Ceramic Balls
### 1. Raw Material Selection
The manufacturing process begins with selecting high-quality ceramic powders. Common materials include:
– Alumina (Al2O3)
– Zirconia (ZrO2)
– Silicon nitride (Si3N4)
– Silicon carbide (SiC)
### 2. Powder Preparation
The ceramic powder is carefully processed to achieve:
– Uniform particle size distribution
– Proper chemical composition
– Optimal purity levels
### 3. Forming Methods
Several techniques are used to form ceramic balls:
#### Isostatic Pressing
Cold isostatic pressing (CIP) applies uniform pressure from all directions to create green bodies with consistent density.
#### Injection Molding
Fine ceramic powder is mixed with binders and injected into spherical molds under high pressure.
#### Rolling Process
Pre-formed ceramic blanks are rolled between rotating plates to achieve spherical shapes.
### 4. Sintering
The formed green balls undergo high-temperature sintering (typically 1400-1800°C) to:
– Remove organic binders
– Achieve full densification
– Develop final mechanical properties
### 5. Precision Grinding
After sintering, the balls undergo precision grinding to:
– Achieve exact dimensional tolerances
– Improve surface finish
– Meet specified sphericity requirements
### 6. Quality Control
Rigorous testing ensures:
– Diameter accuracy (±0.1 μm for high-grade balls)
– Surface roughness (Ra < 0.01 μm for precision applications)
– Mechanical properties (hardness, strength)
– Material purity
## Applications of Ceramic Balls
### Bearings
Ceramic balls are widely used in high-performance bearings for:
– Machine tool spindles
– Aerospace applications
– Medical equipment
– High-speed applications
### Valves and Pumps
Their chemical resistance makes them ideal for:
– Chemical processing equipment
– Oil and gas applications
– Semiconductor manufacturing
### Grinding Media
Ceramic balls serve as grinding media in:
– Paint and pigment production
– Pharmaceutical manufacturing
– Food processing
Keyword: ceramic ball
### Other Applications
– Precision measurement devices
– Ball screws and linear guides
– Decorative purposes
– Spacecraft components
## Advantages of Ceramic Balls
Property | Benefit
High hardness | Excellent wear resistance
Low density | Reduced centrifugal forces in high-speed applications
Corrosion resistance | Long service life in harsh environments
Electrical insulation | Suitable for electronic applications
Non-magnetic | Ideal for sensitive instrumentation
## Future Trends
The ceramic ball industry continues to evolve with:
– Development of new ceramic compositions
– Improved manufacturing techniques for higher precision
– Expanded applications in renewable energy systems
– Growing demand in electric vehicle components
As technology advances, ceramic balls will play an increasingly important role in precision engineering applications across multiple industries.