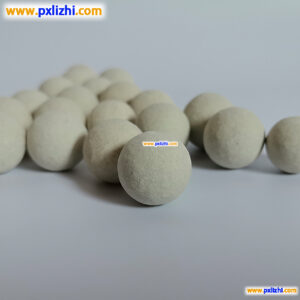
。
# Ceramic Ball Manufacturing Process
## Introduction to Ceramic Balls
Ceramic balls are widely used in various industries due to their excellent properties such as high hardness, wear resistance, and chemical stability. The manufacturing process of ceramic balls involves several precise steps to ensure quality and performance.
## Raw Material Preparation
The first step in ceramic ball manufacturing is the preparation of raw materials. High-purity ceramic powders, such as alumina (Al2O3) or zirconia (ZrO2), are selected based on the desired properties of the final product. These powders are carefully measured and mixed with binders and other additives to form a homogeneous mixture.
## Forming Process
Once the raw materials are prepared, the next step is forming the ceramic balls. There are several methods for forming ceramic balls, including:
– Dry Pressing: The powder mixture is compressed in a mold under high pressure to form green balls.
– Isostatic Pressing: The powder is placed in a flexible mold and subjected to uniform pressure from all directions.
– Extrusion: The mixture is forced through a die to form cylindrical shapes, which are then cut and rounded into balls.
## Drying
After forming, the green ceramic balls contain moisture and binders that need to be removed. The drying process involves controlled heating to evaporate the moisture without causing cracks or deformations. This step is crucial to ensure the structural integrity of the balls before sintering.
## Sintering
Sintering is the most critical step in the ceramic ball manufacturing process. The dried green balls are heated to a high temperature below their melting point, causing the particles to bond together and form a dense, strong structure. The sintering temperature and duration depend on the ceramic material used.
## Grinding and Polishing
Keyword: ceramic ball
After sintering, the ceramic balls may have slight imperfections or rough surfaces. Precision grinding and polishing are performed to achieve the desired size, roundness, and surface finish. This step ensures that the balls meet strict dimensional and geometric tolerances.
## Quality Control
Quality control is an integral part of the ceramic ball manufacturing process. Each batch of balls undergoes rigorous testing, including:
– Dimensional inspection
– Roundness measurement
– Surface finish analysis
– Mechanical property testing
Only balls that meet the specified standards are approved for shipment to customers.
## Applications of Ceramic Balls
Ceramic balls are used in various applications, including:
– Bearings for high-speed and high-temperature environments
– Valves and pumps in corrosive or abrasive conditions
– Grinding media in ball mills
– Precision components in aerospace and medical devices
## Conclusion
The manufacturing process of ceramic balls requires precision and attention to detail at every stage. From raw material preparation to final quality control, each step contributes to the production of high-performance ceramic balls that meet the demanding requirements of modern industries.