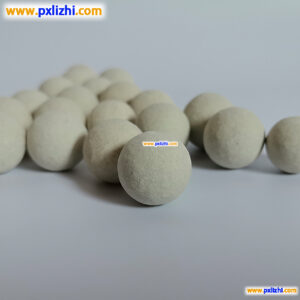
# Ceramic Ball Manufacturing Process and Applications
## Introduction to Ceramic Balls
Ceramic balls are high-performance spherical components made from advanced ceramic materials. These precision-engineered balls offer exceptional properties that make them suitable for a wide range of industrial applications. Their manufacturing process requires specialized techniques to achieve the required dimensional accuracy and material properties.
Keyword: ceramic ball
## Manufacturing Process of Ceramic Balls
### 1. Raw Material Preparation
The production of ceramic balls begins with the selection of high-quality raw materials. Common ceramic materials used include:
– Alumina (Al2O3)
– Zirconia (ZrO2)
– Silicon nitride (Si3N4)
– Silicon carbide (SiC)
These materials are carefully measured and mixed with binders and additives to create a homogeneous mixture.
### 2. Forming Process
There are several methods to form ceramic balls:
– Dry pressing: Powder is compressed in spherical molds
– Isostatic pressing: Uniform pressure is applied from all directions
– Extrusion and spheronization: Material is extruded and then rounded
– Slip casting: Ceramic slurry is poured into spherical molds
### 3. Sintering
The formed green balls undergo sintering in high-temperature furnaces:
– Temperature ranges from 1400°C to 1800°C depending on material
– Process duration varies from several hours to days
– Controlled atmosphere (air, nitrogen, or vacuum) may be required
### 4. Grinding and Lapping
After sintering, the balls undergo precision finishing:
– Diamond grinding wheels achieve dimensional accuracy
– Lapping process improves surface finish
– Final tolerances can reach within 0.1 microns
### 5. Quality Control
Rigorous quality checks ensure product consistency:
– Dimensional measurements
– Surface roughness evaluation
– Hardness testing
– Roundness verification
## Applications of Ceramic Balls
### Bearings
Ceramic balls are widely used in high-performance bearings:
– Hybrid bearings (ceramic balls with steel races)
– Full ceramic bearings
– Applications in aerospace, medical, and semiconductor equipment
### Valves and Pumps
Their chemical resistance makes them ideal for:
– Ball valves in corrosive environments
– Metering pumps
– Chemical processing equipment
### Grinding Media
Ceramic balls serve as grinding media in:
– Paint and pigment production
– Pharmaceutical manufacturing
– Food processing
### Other Applications
Additional uses include:
– Precision instruments
– Automotive components
– Defense applications
– Semiconductor manufacturing equipment
## Advantages of Ceramic Balls
The unique properties of ceramic balls provide several benefits:
– High hardness and wear resistance
– Excellent corrosion resistance
– Low density (40-60% of steel)
– Electrical insulation properties
– High temperature capability
– Non-magnetic characteristics
## Future Trends in Ceramic Ball Technology
The ceramic ball industry continues to evolve with:
– Development of new ceramic compositions
– Improved manufacturing techniques for higher precision
– Expansion into new application areas
– Cost reduction through process optimization
As technology advances, ceramic balls are expected to play an increasingly important role in high-performance mechanical systems across various industries.