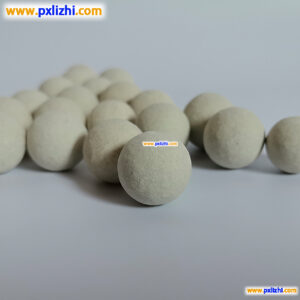
# Ceramic Ball Manufacturing Process and Applications
## Introduction to Ceramic Balls
Ceramic balls are highly specialized spherical components made from various ceramic materials. These precision-engineered spheres offer exceptional properties that make them valuable across multiple industries. Their unique characteristics stem from the manufacturing process and the ceramic materials used in their production.
## The Manufacturing Process of Ceramic Balls
### 1. Raw Material Preparation
The ceramic ball manufacturing process begins with the selection and preparation of raw materials. Common ceramic materials used include:
– Alumina (Al2O3)
– Zirconia (ZrO2)
– Silicon nitride (Si3N4)
– Silicon carbide (SiC)
These materials are carefully measured and mixed with binders and additives to create a homogeneous mixture suitable for forming.
### 2. Forming Process
Several methods are employed to form ceramic balls:
– Dry pressing: Powder is compressed in spherical molds
– Isostatic pressing: Uniform pressure is applied from all directions
– Extrusion: Material is forced through dies and cut into spherical shapes
– Slip casting: Liquid ceramic slurry is poured into spherical molds
### 3. Sintering
The formed green balls undergo high-temperature sintering (typically 1400-1700°C) to achieve:
– Densification of the ceramic structure
– Development of final mechanical properties
– Removal of organic binders
– Shrinkage to final dimensions
### 4. Precision Grinding and Polishing
After sintering, ceramic balls undergo precision grinding and polishing to achieve:
– Tight dimensional tolerances (often within microns)
– Superior surface finish (Ra < 0.01 μm)
– Perfect spherical geometry
– Consistent size distribution
### 5. Quality Control
Rigorous quality checks ensure:
– Diameter consistency
– Surface quality
– Mechanical properties
– Chemical composition verification
## Key Properties of Ceramic Balls
Ceramic balls possess several advantageous properties:
– High hardness (up to 2000 HV)
– Excellent wear resistance
– Corrosion resistance
– High temperature stability
– Electrical insulation
– Low density (compared to metals)
– Non-magnetic characteristics
## Applications of Ceramic Balls
### 1. Bearing Applications
Ceramic balls are widely used in high-performance bearings for:
– Machine tool spindles
– Aerospace components
– Medical equipment
– High-speed applications
– Corrosive environments
### 2. Valve Components
In valve applications, ceramic balls provide:
– Exceptional wear resistance
– Chemical inertness
– Long service life
– Reliable sealing
Keyword: ceramic ball
### 3. Grinding Media
Ceramic balls serve as grinding media in:
– Paint and pigment production
– Pharmaceutical manufacturing
– Food processing
– Mineral processing
### 4. Other Specialized Applications
Additional uses include:
– Flow control devices
– Measurement standards
– Semiconductor manufacturing
– Nuclear applications
– Space technology
## Advantages Over Metal Balls
Ceramic balls offer several benefits compared to their metal counterparts:
– Longer service life (3-5 times longer than steel)
– Reduced maintenance requirements
– Higher speed capabilities
– Lower friction coefficients
– Better performance in extreme environments
– Lighter weight (up to 60% lighter than steel)
## Future Trends in Ceramic Ball Technology
The ceramic ball industry continues to evolve with:
– Development of new ceramic compositions
– Improved manufacturing techniques
– Nanotechnology applications
– Enhanced quality control methods
– Expansion into new industrial sectors
As material science advances, ceramic balls are expected to play an increasingly important role in high-tech applications where performance and reliability are critical.