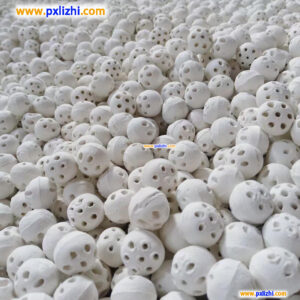
# Alumina Ceramic Ball Applications and Properties
## Introduction to Alumina Ceramic Balls
Alumina ceramic balls are high-performance ceramic spheres made from aluminum oxide (Al₂O₃). These precision-engineered components have become essential in various industrial applications due to their exceptional properties and durability. With alumina content typically ranging from 90% to 99.9%, these ceramic balls offer superior performance compared to traditional metal alternatives.
## Key Properties of Alumina Ceramic Balls
### 1. Exceptional Hardness and Wear Resistance
Alumina ceramic balls rank among the hardest materials available, second only to diamond in some formulations. This extreme hardness translates to outstanding wear resistance, making them ideal for applications involving friction and abrasion.
### 2. High Temperature Stability
These ceramic balls maintain their structural integrity at temperatures up to 1600°C (2912°F), far exceeding the capabilities of most metal alloys. This thermal stability prevents deformation and maintains performance in extreme environments.
### 3. Chemical Inertness
Alumina ceramic balls demonstrate remarkable resistance to acids, alkalis, and organic solvents. This chemical inertness makes them suitable for corrosive environments where metal components would degrade rapidly.
### 4. Electrical Insulation
With excellent dielectric properties, alumina ceramic balls serve as effective electrical insulators in high-voltage applications. Their resistivity remains stable across a wide temperature range.
### 5. Low Density
Keyword: alumina ceramic ball
Weighing approximately 60% less than steel counterparts, alumina ceramic balls reduce rotational inertia in moving systems, leading to energy savings and improved efficiency.
## Industrial Applications of Alumina Ceramic Balls
### 1. Bearings and Precision Components
Alumina ceramic balls are widely used in high-performance bearings for applications requiring extreme precision, high speeds, or operation in corrosive environments. Industries such as aerospace, medical equipment, and semiconductor manufacturing rely on these components.
### 2. Grinding Media
In the mining and pigment industries, alumina ceramic balls serve as grinding media in ball mills. Their hardness and wear resistance make them more efficient than traditional steel balls, reducing contamination and improving product purity.
### 3. Valve Components
The chemical resistance of alumina ceramic balls makes them ideal for valve components in aggressive fluid handling systems, including chemical processing, oil and gas, and water treatment applications.
### 4. Electronics and Insulation
In the electronics industry, alumina ceramic balls provide electrical insulation in high-voltage equipment and serve as spacers in sensitive electronic assemblies where thermal and electrical isolation are critical.
### 5. Medical Applications
The biocompatibility of high-purity alumina ceramic balls has led to their use in orthopedic implants and dental applications, where their wear resistance and chemical stability are essential for long-term performance.
## Manufacturing Considerations
Alumina ceramic balls are produced through advanced manufacturing processes including isostatic pressing, sintering, and precision grinding. The production method significantly impacts the final properties, with higher alumina content (99%+) offering superior performance but at increased cost. Surface finish and dimensional tolerances are critical factors that determine suitability for specific applications.
## Conclusion
Alumina ceramic balls represent a versatile engineering solution that combines exceptional mechanical, thermal, and chemical properties. As technology advances and industries demand higher performance materials, the applications for these precision ceramic components continue to expand across multiple sectors. Their unique combination of properties makes them indispensable in environments where conventional materials fail to meet performance requirements.